ОТВОДЫ
Стальные отводы – это один из основных конструктивных элементов трубопровода, который позволяет создать максимально надежную конструкцию трубопровода, змеевика нужной формы, в том числе в ограниченном пространстве.
Отводы обеспечивают целостность и надежность конструкции.
НАШИ ТЕХНИЧЕСКИЕ ВОЗМОЖНОСТИ ПОЗВОЛЯЮТ ИЗГОТАВЛИВАТЬ ОТВОДЫ:
Технические характеристики
|
Минимальные размеры
|
Максимальные размеры
|
Диаметр, Ø
|
57
|
219
|
Толщина стенки, S
|
3,5
|
12
|
Радиус, R
|
1,0 DN
|
1,5 DN
|
Используемые марки стали:
- 10, 20, 20А, 20-ПВ, 20ЮЧ, 20ФА;
- 13ХФА, 20ХФА, 15ХФ, 15ХФА;
- 10Г2, 14ХГС, 15ГС, 16ГС, 17ГС, 17Г1С, 17Г1СУ, 09Г2С;
АО «Нефтемаш» изготавливает отводы методом горячей протяжки трубных заготовок мерной длины по рогообразному сердечнику с последующими операциями горячей объемной правки и калибровки отводов. Такой способ позволяет получать отводы с малым радиусом кривизны и равной по всему объему изделия толщиной стенки. Технологический процесс рассчитан на получение крутоизогнутых отводов из мерных труб заготовок и состоит из нескольких этапов многооперационной маршрутной технологии:
1. резка труб на мерные заготовки, резка патрубков, т.е. заготовок труб определенного размера
2. горячая протяжка, протягивание заготовки на специальных гидропрессах по рогообразному сердечнику, который создает необходимую форму.
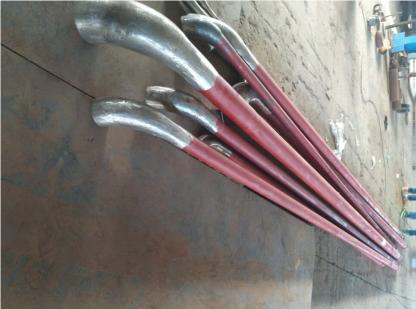
Схема процесса протяжки отводов на рогообразном сердечнике:
- штанга 1
- формообразующий участок 2
- калибрующий участок 3 с заданным радиусом кривизны
3. горячая объемная правка, калибровка в вертикальных гидравлических прессах.
4. обработка присоединительных торцов под сварку и калибровка отводов по внутреннему диаметру. В ходе калибровки корректируются геометрические размеры, что в первую очередь касается диаметра. В завершении отводы обрабатываются на торцовочных станках.
Качество изготовленного методом горячей протяжки отвода в АО «Нефтемаш» подтверждается комплексом механических испытаний в аттестованной и аккредито-ванной лаборатории. Объем испытаний зависит от условий, в которых эксплуати-руется изготовленное изделие.